November 8, 2016 at 12:07 PM
Print Buyer's Guide to UV Coating
Have you ever received a postcard in the mail or picked up a brochure that was so glossy it almost seemed as if it were still wet? That super glossy sheen is a UV, or Ultraviolet, coating. Advances in print coating technology means there are more options now than ever before, and more to know. The following is a quick reference guide for print buyers and marketing professionals.
UV Coating Benefits
Coatings can be applied in-line on press, or off-line on a separate piece of equipment. The coating can be applied as a flood covering the entire sheet, or as a spot. This allows designers greater flexibility in how they utilize coatings to enhance images.
* Provides superior protection from scuffs and scratches and is water and chemical resistant, making UV an ideal choice for protecting your Direct Mail pieces like postcards and self-mailers.
* UV coatings have a high clarity and do not yellow over time.
* Free of solvents, UV does not emit volatile organic compounds (VOCs) eliminating the unpleasant odor that sometimes builds up inside cartons of printed materials.
* Instant curing means no drying time, allowing press sheets to immediately proceed to bindery for cutting, scoring, folding, etc. This is especially useful in short-run, quick-turn digital printing.
Sheen/Finish
Coating comes in clear satin, matte, gloss, and high gloss. There are also coatings available with special formulations to achieve unique effects. Some of these include:
* Phosphorescent UV - absorbs light to produce a glow in the dark effect.
* Sandpaper UV - grainy particles added to the coating produces a gritty texture.
* Switch UV - microparticles suspended in the coating add shimmer and a color changing effect.
* Pearlescent UV - pigments added to the coating create iridescence.
* Micro-encapsulated Scented UV - produces scratch-n-sniff scents.
* Glitter UV - contains reflective particles to make the coating sparkle.
* Raised UV - adds dimension and texture, making details stand out visually and tactilely. Raised UV is also commonly referred to as 3D UV and Embossed UV.
How the UV Printing Process Works
UV coatings are applied wet and when exposed to ultraviolet light cures in milliseconds due to a chemical reaction called chain polymerisation. Ultraviolet radiation causes acrylates to bond, forming a plastic film which protects against scuffing, scratches and fingerprints. It also adds sheen and smoothness.
Printing Tips
* UV coating works best on coated, cover weight paper stocks.* The minimum paper requirement is 80# text.
* Fingerprints show more over dark areas of print. This is worth remembering during creative and graphic design.
* Raised UV can sometimes crack during cutting and folding depending on the thickness of the coating. As a rule, keep Raised UV ⅛” away from scores, trims, folds, and edges.
* Knock out any areas where glue will be applied such as the flaps on pocket folders, or where people will be writing such as on reply devices.
* Gloss UV applied as a flood over a coating of spot dull varnish is called strike-through and results in the areas where the dull varnish was applied remaining dull while the rest of the image is glossy, creating added contrast to make details pop.
With the variety of UV products available, designers and marketers have great freedom to create print with stunning visuals, impactful imagery, and sensory experiences. Used individually or in combination, coatings can help produce amazing results. Not all printers have UV coating capabilities, and many that do are limited to the most basic flood coating in satin or gloss. Taking advantage of the full range of UV products requires working with an experienced UV printer that specializes in producing award winning commercial print, like The John Roberts Company.
Popular Posts
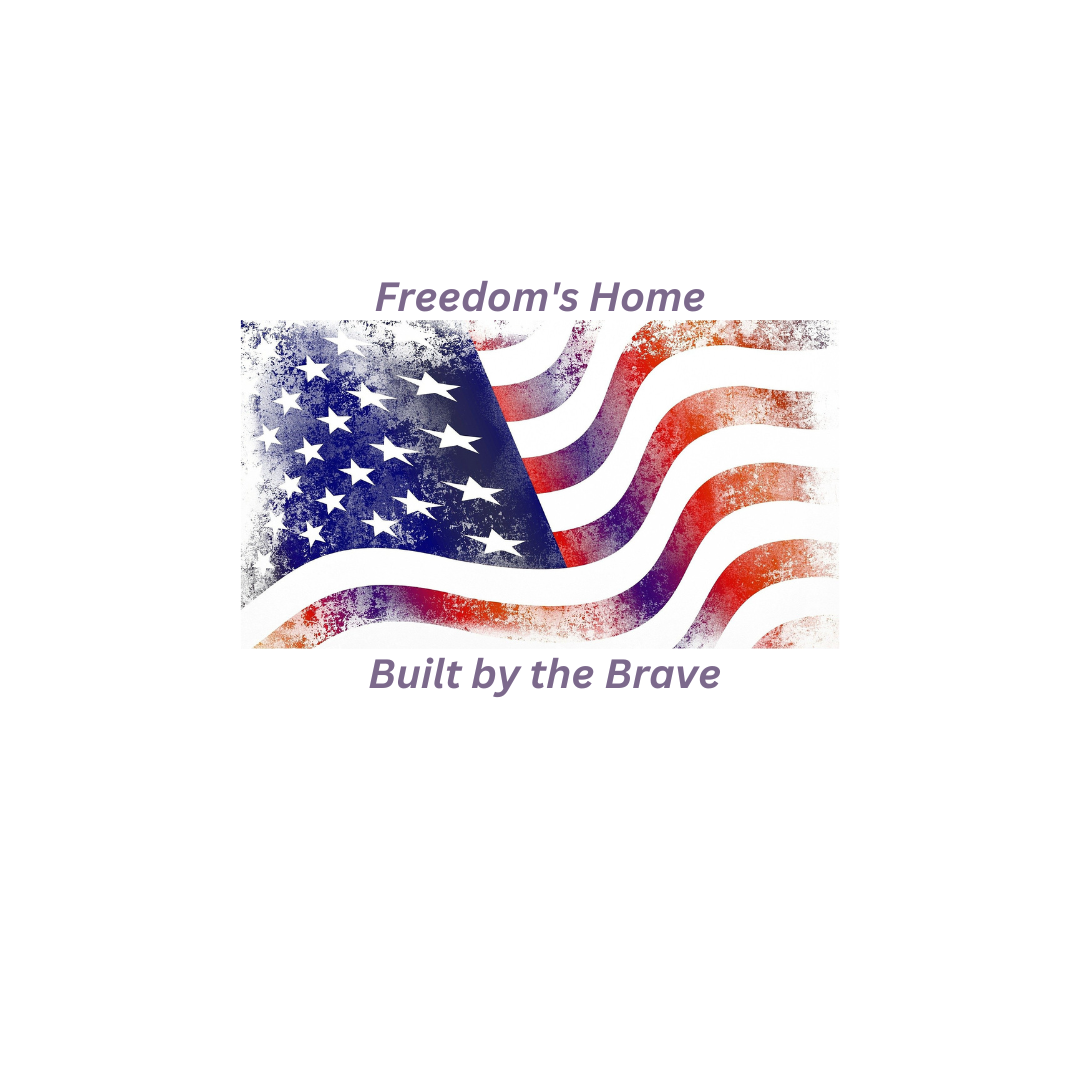
Memorial Weekend
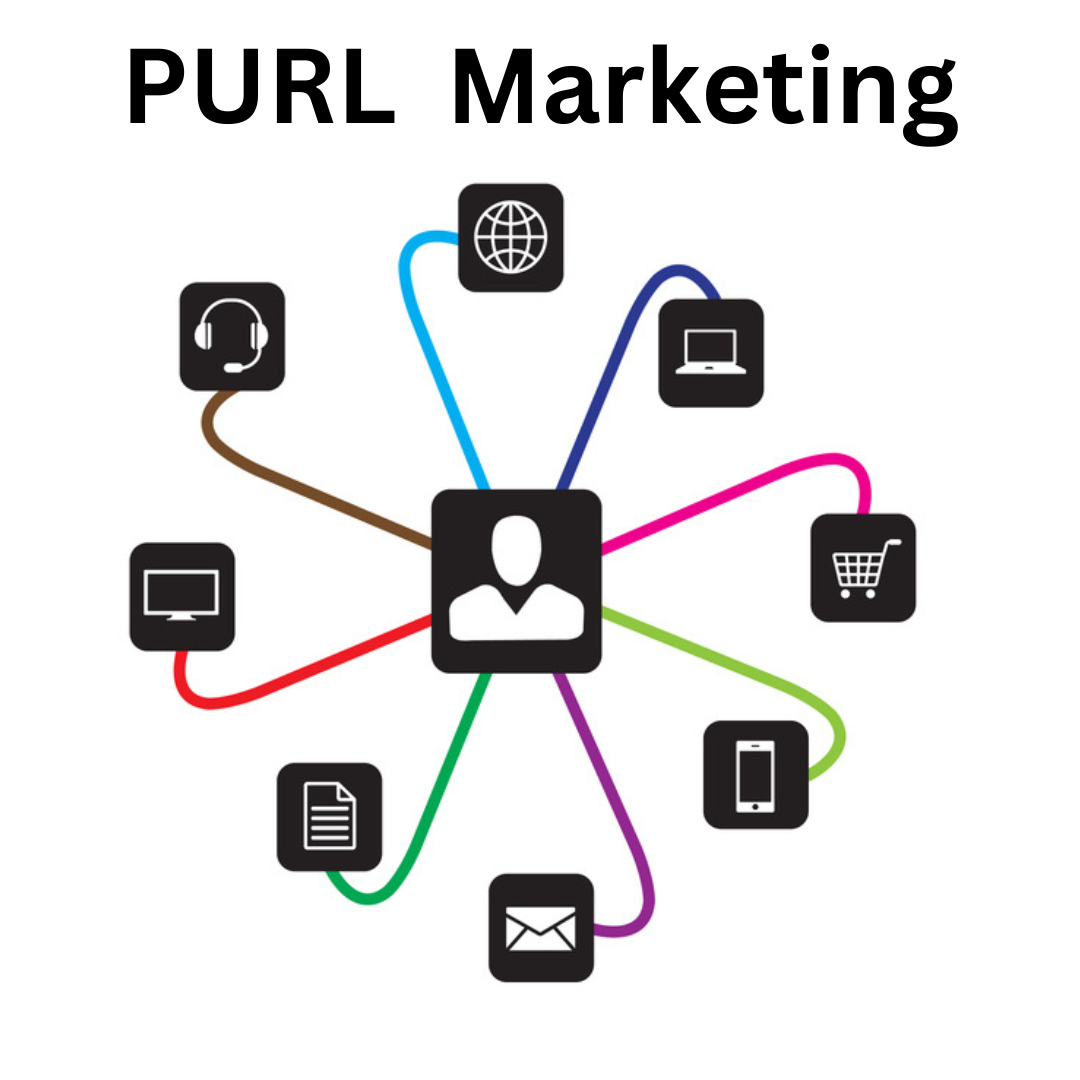
Landing Pages
Learn Why Omnichannel Marketing is Trending
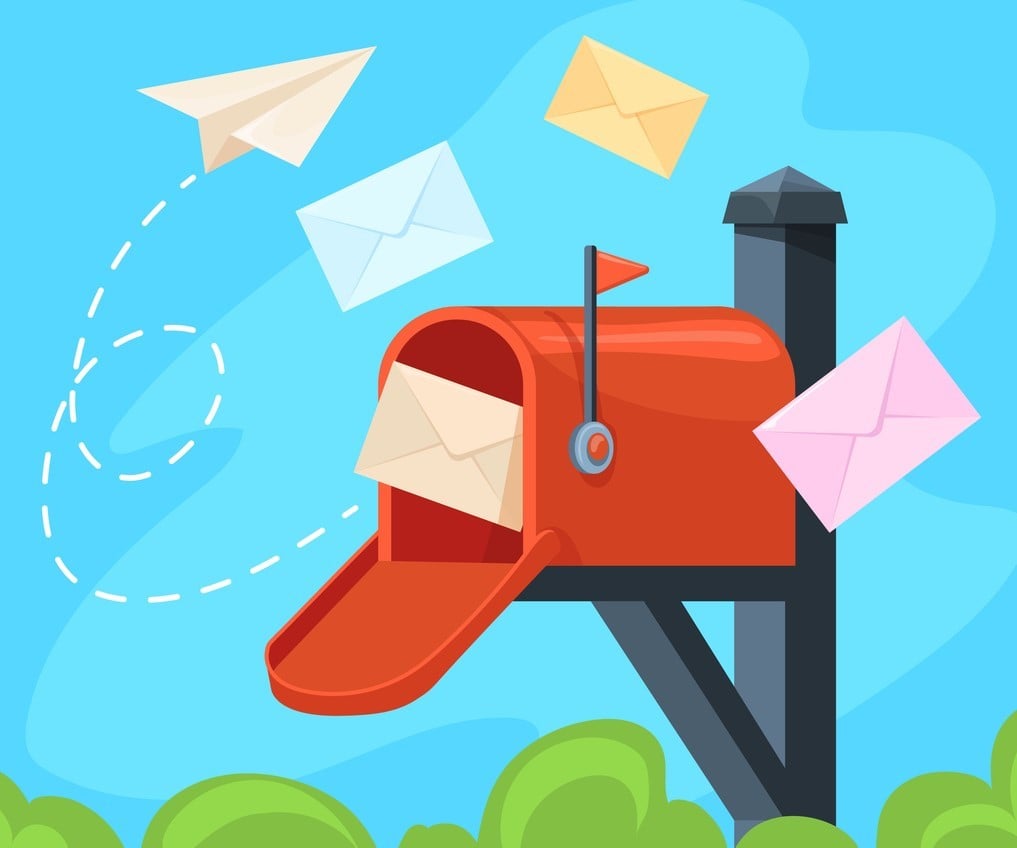
Direct Mail